Ever stepped on a squeaky floorboard and felt a sudden jolt of anxiety about the structural integrity of your home? Or perhaps you’ve noticed a warped, undulating wood floor and wondered what could be causing the strange deformation. The answer might lie beneath your feet, in the often-overlooked foundation of your home: the concrete slab.

Image: tarabasoftware.com
Installing wood floors directly onto concrete poses a unique challenge due to the inherent permeability of concrete. Moisture can travel from the ground, through the concrete, and into your beloved wood flooring, leading to warping, buckling, and even rot. This is where a moisture barrier comes into play, acting as a crucial shield against the insidious threat of moisture and preserving the integrity of your beautiful wood floors.
Understanding the Importance of a Moisture Barrier
A moisture barrier, also known as a vapor barrier, is a thin membrane installed between the concrete slab and the wood subfloor, acting as a barrier against moisture migrating from the concrete. This seemingly simple addition can be the difference between a long-lasting, beautiful wood floor and a costly, frustrating restoration project.
Why Is Moisture So Detrimental to Wood Flooring?
Wood is a hygroscopic material, meaning it readily absorbs and releases moisture from the surrounding environment. When moisture seeps into wood flooring from a concrete slab, it can lead to a cascade of problems:
- Warpage and Bucking: As wood absorbs moisture, it expands. This uneven expansion can cause the floorboards to warp and buckle, creating unsightly dips and unevenness.
- Rot and Decay: Excessive moisture provides a breeding ground for mold, mildew, and wood-rotting fungi. These microorganisms can quickly damage the wood, weakening its structure and creating unpleasant odors.
- Squeaking and Noises: As wood expands and contracts due to moisture fluctuations, it can rub against other components of the floor, producing annoying squeaking and creaking noises.
Not All Concrete is Created Equal
The level of moisture in concrete can vary widely depending on factors like:
- Climate: High humidity and frequent rainfall can increase the moisture content in concrete.
- Soil Conditions: Clay soils, known for their moisture retention, can contribute to a higher moisture level in the slab.
- Construction Practices: Improper curing of concrete and inadequate ventilation can lead to trapped moisture within the slab.
Regardless of the source, even seemingly minor moisture levels can have a significant impact on wood flooring. This is where a moisture barrier steps in to protect your investment and prevent such issues from arising.
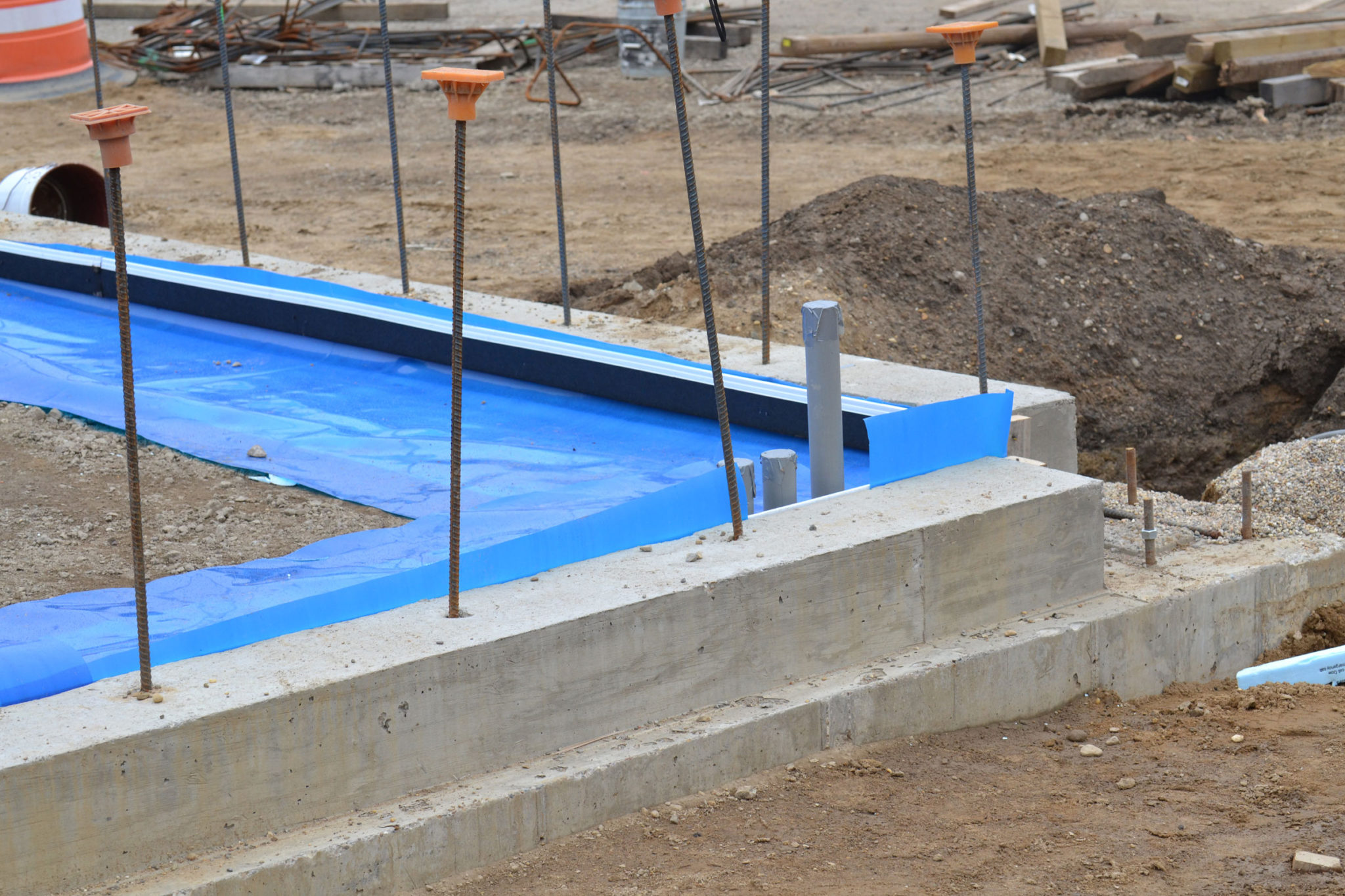
Image: gbdmagazine.com
Choosing the Right Moisture Barrier
Not all moisture barriers are created equal. Selecting the right barrier for your project depends on a few key factors:
1. Vapor Retardation Class (RC)
The vapor retardation class (RC) indicates the barrier’s effectiveness in preventing moisture transmission. A higher RC rating signifies a more effective barrier. For wood floors on concrete, an RC rating of at least 15 is recommended.
2. Durability and Installation Requirements
Different moisture barrier materials offer varying levels of durability and installation methods. Some common choices include:
- Polyethylene (PE) Sheeting: Affordable and readily available, but lacks the strength and durability of other options.
- Polypropylene (PP) Sheeting: Stronger and more tear-resistant than PE sheeting, but slightly more expensive.
- Foil-faced Insulation: Provides both vapor barrier and thermal insulation, but requires special installation techniques.
- Concrete Densifier: A liquid solution that penetrates the concrete and reduces its permeability, but may not be suitable for all applications.
3. Local Regulations and Building Codes:
It’s essential to research and comply with local building codes and regulations regarding moisture barrier requirements in your area.
Installing Your Moisture Barrier: A Step-by-Step Guide
Proper installation is paramount for a moisture barrier to effectively protect your wood floors. Follow these general guidelines for a successful installation:
1. Prepare the Concrete Slab
Before laying down the moisture barrier, ensure the concrete slab is clean, smooth, and free from any debris or unevenness. Any cracks or imperfections should be repaired using a suitable sealant or patching compound.
2. Lay Down The Moisture Barrier
Unroll the chosen moisture barrier material and ensure it covers the entire concrete surface. Overlap the seams by at least 6 inches to create a continuous seal and prevent potential leaks.
3. Secure the Moisture Barrier
Secure the moisture barrier in place using heavy-duty tape, staples, or a combination of both methods. Ensure the barrier is securely attached to the concrete slab, with no gaps or loose areas.
4. Install the Subfloor
With the moisture barrier in place, you can install the wood subfloor. The subfloor acts as the foundation for the finished wood flooring. Follow industry standards for subfloor installation, ensuring proper spacing and nailing techniques.
Beyond the Barrier: Additional Strategies for Moisture Control
While a moisture barrier is a fundamental step in protecting your wood floors from moisture, it’s not the sole solution. Incorporating these additional strategies further enhances your moisture control efforts:
1. Adequate Ventilation:
Ensure the crawl space or basement beneath your home is well-ventilated. Proper ventilation allows moisture to escape, preventing its accumulation within the foundation.
2. Dehumidification:
In high-humidity environments, using a dehumidifier can help control moisture levels by removing excess humidity from the air. This is particularly helpful during humid seasons or when the basement or crawl space lacks adequate ventilation.
3. Concrete Sealer:
Applying a concrete sealer can further reduce the permeability of the concrete slab, further minimizing moisture transmission. Select a sealer specifically designed for concrete floors and follow the manufacturer’s instructions for application.
Maintaining Your Moisture Barrier and Wood Floors
Once your moisture barrier and wood floors are installed, it’s important to maintain them to ensure their longevity:
- Monitor Moisture Levels: Periodically monitor the moisture levels in your basement or crawl space using a moisture meter. This will help detect any potential issues with moisture intrusion.
- Regular Cleaning: Keep your wood floors clean and dust-free, as accumulated dirt and debris can trap moisture and create a breeding ground for mold and mildew.
- Prevent Water Damage: Be vigilant in preventing water leaks from pipes or appliances. Quickly address any water spills or leaks to minimize the risk of damage to your wood floors.
Moisture Barrier For Wood Floors On Concrete
Investing in a Moisture Barrier: A Wise Decision
Installing a moisture barrier might seem like a small detail, but it’s a crucial investment in the longevity and beauty of your wood floors. By effectively preventing moisture from migrating from the concrete slab, you can significantly reduce the risk of warping, buckling, rot, and other issues that can lead to costly repairs and replacements.
Remember, moisture control is an ongoing process that requires both proactive measures and regular maintenance. By understanding the importance of a moisture barrier and implementing proper installation and maintenance practices, you can ensure your wood floors remain resilient, beautiful, and a source of pride for years to come.