Have you ever wondered what goes into making the steel that forms the backbone of our modern world? It starts with raw materials, and one of the most important is pig iron. But not all pig iron is created equal. There’s a special type known as DF pig iron, which stands for “Directly Reduced Pig Iron,” and it plays a crucial role in the global steel industry.
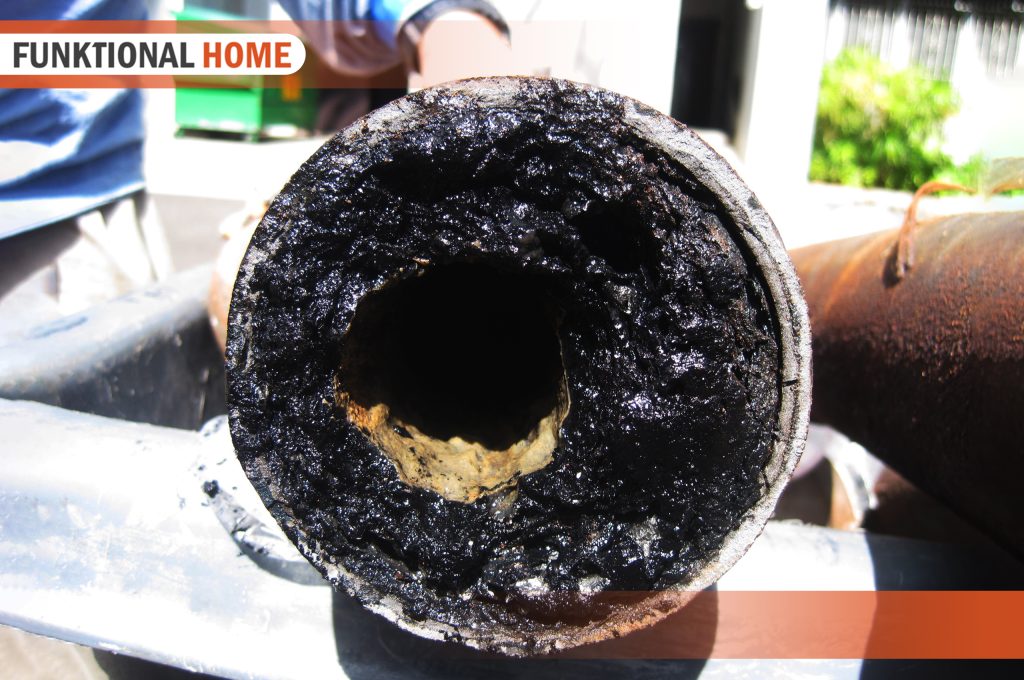
Image: www.funktionalhome.com
DF pig iron is a fascinating material that’s both old and new. It’s a variation on traditional pig iron, a product of iron ore smelting that dates back centuries. However, the “direct reduction” process that gives DF pig iron its name is a relatively recent innovation. This article will delve into the world of DF pig iron, exploring its history, production, properties, uses, and impact on the steel industry.
A Glimpse into the History of Iron and Steel
Before we dive into the details of DF pig iron, let’s rewind the clock and understand the historical context. Iron has been used for thousands of years. Early humans discovered that they could smelt iron ore, a naturally occurring mineral, using charcoal fires. This process produced iron metal, which was then hammered and shaped into tools and weapons.
The invention of the blast furnace in the 14th century revolutionized iron production. Blast furnaces allowed for much larger-scale iron production, leading to the era of industrialization. These furnaces used hot air to intensify the smelting process, yielding molten iron called “pig iron.” Pig iron served as the primary raw material for making steel, a stronger and more versatile metal.
Pig Iron: The Foundation of Steel
Pig iron is essentially iron that contains impurities, primarily carbon. The carbon content varies depending on the production process, but it typically ranges from 2% to 4%. Pig iron produced in blast furnaces is known as “hot metal,” which is then poured into molds to solidify. The solidified pig iron is transported to steel mills for further processing.
The Emergence of Direct Reduced Iron (DRI)
In the late 20th century, a new method of iron production emerged called “direct reduction.” This process bypasses the blast furnace altogether. In direct reduction, iron ore is treated with a reducing gas, such as natural gas or coal gas, at high temperatures. This process removes oxygen from the iron oxide in the ore, leaving behind a solid, porous iron product called “direct reduced iron” or DRI.
DRI production is becoming increasingly popular for several reasons. First, it allows for the use of lower-grade iron ore that may be unsuitable for blast furnaces. Second, it consumes less energy than traditional blast furnace production. Third, it emits fewer greenhouse gases, making it a more environmentally friendly option.

Image: dir.indiamart.com
DF Pig Iron: A Bridge Between Tradition and Innovation
DF pig iron, also known as “Directly Reduced Pig Iron,” is a variation of DRI that’s specifically designed for use in steelmaking. It’s made by subjecting DRI to a melting process, which transforms the solid iron into a liquid form. This molten DF pig iron possesses several advantages over traditional hot metal:
- Higher purity: DF pig iron typically has a lower carbon content and fewer impurities than hot metal.
- Greater flexibility: DF pig iron can be easily adjusted for different steelmaking processes, resulting in more control over the final product.
- Environmental friendliness: The production of DF pig iron is often more energy-efficient and results in fewer greenhouse gas emissions compared to traditional methods.
The Benefits of DF Pig Iron in Steelmaking
The unique characteristics of DF pig iron make it a valuable input for steel production. Here are some key benefits:
- Enhanced steel quality: DF pig iron’s lower impurity levels lead to higher-quality steel with improved strength, ductility, and corrosion resistance. This is crucial for various steel applications, including construction, automotive, and shipbuilding.
- Increased efficiency: DF pig iron is typically more easily meltable compared to hot metal, which can improve the efficiency of steel production. The faster melting times reduce energy consumption and production costs.
- Greater versatility: DF pig iron can be used in various steelmaking methods, including electric arc furnaces (EAFs), basic oxygen furnaces (BOFs), and ladle furnaces. This flexibility gives steelmakers more options to tailor steel production to specific needs.
The Global Importance of DF Pig Iron
The demand for DF pig iron is rising globally, particularly in countries with rapidly growing steel industries. The demand for high-quality steel is increasing, and DF pig iron provides a solution for producing superior steel products. Additionally, the environmental concerns surrounding traditional steelmaking methods are driving the transition towards cleaner and more sustainable practices such as DRI and DF pig iron production.
The Future of DF Pig Iron
As the global emphasis on sustainability grows, DF pig iron is expected to play an even more prominent role in the future. Research and development are ongoing to improve the process efficiency, reduce costs, and further enhance the environmental benefits of DF pig iron production. We can expect to see continued growth in the use of DF pig iron in the coming years, contributing to a more sustainable and innovative steel industry.
Df Pig Iron
Conclusion
From its roots in traditional ironmaking to its emergence as a key ingredient in modern steel production, DF pig iron is a testament to the ongoing evolution of materials science. Its unique properties, efficiency, and environmental benefits make it an essential component for the future of steelmaking. As we continue to strive for sustainability and innovation, DF pig iron stands at the forefront of the journey toward a brighter and stronger future for the steel industry.