Imagine a workshop humming with the rhythmic whir of a powerful lathe, metal shavings cascading downwards in a silvery shower. A scene familiar to many, yet beneath the surface lurks a silent danger – the invisible mist that forms as the machine works its magic. This mist, seemingly innocuous, carries with it a cocktail of potentially hazardous substances capable of inflicting long-term harm on the unsuspecting worker. This article delves into the world of lathe accident mist, its composition, health risks, and the crucial steps needed to mitigate its impact.

Image: sessionpower.com
Lathe accident mist, often referred to as cutting fluid mist or metalworking fluid mist, is a complex aerosol generated during metal cutting operations. It arises from the interaction of cutting fluid, the metal being machined, and the high temperatures created within the cutting zone. This mist readily disperses in the air, making it difficult to perceive, yet it carries a significant threat to the health of machinists and those working in the surrounding environment.
Unveiling the Threat: Composition and Properties of Lathe Accident Mist
The composition of lathe accident mist varies significantly depending on the type of cutting fluid employed, the metal being machined, and the specific conditions of the machining process. Generally, this mist comprises a mix of:
- Cutting Fluid Particles: These are minute droplets of the cutting fluid itself, either primarily water-based, oil-based, or a combination of the two. Each type carries its own set of risks.
- Metal Particles: Tiny, suspended particles of the metal being machined. Their size varies, with some being so fine they are practically invisible, increasing the risk of inhalation.
- Organic Compounds: These can be present in both the cutting fluid and the metal, often released as a result of the heat generated during machining. Many of these compounds are known to be harmful to human health.
- Other Contaminants: The mist can also contain other contaminants like bacteria, fungi, and dust particles, depending on the shop environment.
The properties of lathe accident mist, such as particle size, concentration, and chemical composition, greatly influence its potential health effects. Smaller particles pose a greater risk as they can penetrate deeper into the respiratory system, increasing the chance of reaching the lungs.
The Silent Toll: Health Risks Associated with Lathe Accident Mist
Exposure to lathe accident mist, over time, can lead to a range of health problems, impacting various bodily systems:**
Respiratory Issues
Inhalation of the mist can irritate the airways, causing coughing, wheezing, shortness of breath, and, in severe cases, even pneumonia. Some cutting fluid components can lead to allergic reactions, asthma, and even fibrosis (scarring) of the lungs.
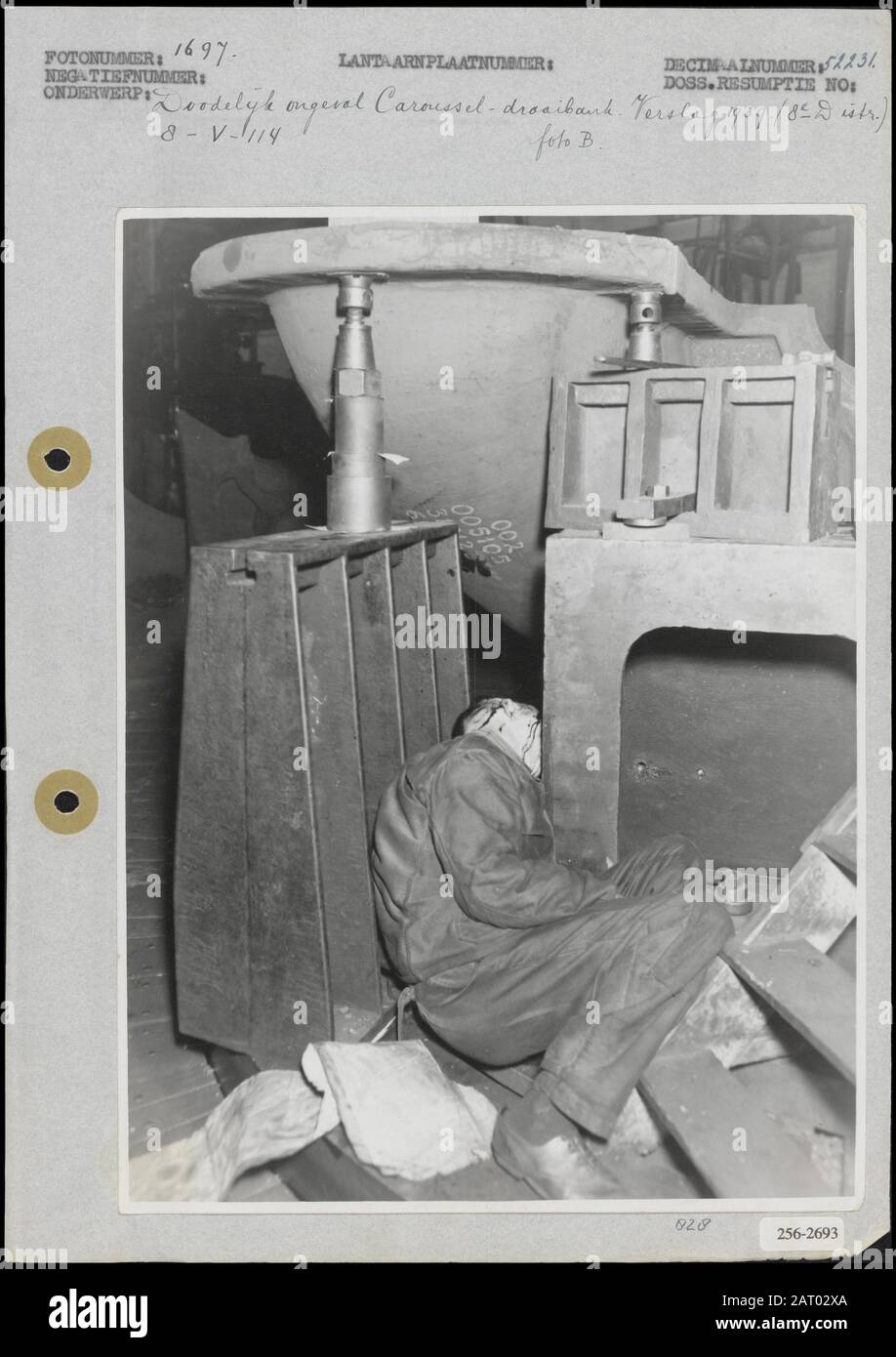
Image: www.alamy.com
Skin Problems
Direct contact with the mist can lead to dermatitis, characterized by redness, itching, and dryness. Repeated exposure can trigger more severe allergic reactions.
Eye Irritation
Eye irritation and conjunctivitis are common due to contact with the mist. Some components can cause lasting eye damage if not quickly treated.
Systemic Effects
Some components, particularly those in oil-based cutting fluids, can be absorbed through the skin and even inhaled, leading to a range of systemic effects like headaches, fatigue, dizziness, and even liver or kidney damage in severe cases.
Cancer Risk
Studies have shown a link between exposure to certain cutting fluid components like mineral oils and an increased risk of cancer, particularly lung and skin cancers. While the evidence is still evolving, the potential for long-term damage is a serious concern.
Mitigating the Risk: Controlling and Reducing Lathe Accident Mist
Recognizing the hazards associated with lathe accident mist, effective control measures are essential to safeguard worker health. A multi-faceted approach is key, encompassing preventative measures, engineering controls, and personal protective equipment (PPE).
Prevention Through Process Modification
Selecting appropriate cutting fluids is a crucial first step. Water-based fluids, though not without risks, generally represent a lower health hazard compared to oil-based counterparts, especially regarding carcinogenic potential.
Minimizing the amount of cutting fluid used and implementing techniques that produce less mist, such as using high-pressure coolant systems, can also drastically reduce exposure.
Engineering Controls: Protecting the Workplace
Engineering controls involve modifying the workplace to reduce mist generation and exposure. Some effective measures include:
- Enclosure Systems: These physically enclose the machining operation, containing the mist within a designated area. Proper ventilation is essential to exhaust the mist safely from the enclosure.
- Local Exhaust Ventilation (LEV): Using LEV systems, such as hoods or downdraft tables, to capture the mist at source is highly effective. It is essential to ensure a sufficient suction force to effectively remove the mist.
- Mist Collection Systems: These systems use filters or other mechanisms to collect the mist before it can disperse into the air. The collected mist should be disposed of safely to prevent environmental contamination.
Personal Protective Equipment (PPE):
A Final Line of Defense
PPE, while an essential precaution, should be considered a last resort after implementing preventative measures and engineering controls. Proper PPE includes:
- Respirators: These devices filter out airborne particles, protecting the respiratory system from inhaled mist. Selecting the right respirator type and ensuring a secure fit are crucial for proper functionality.
- Gloves: Protective gloves should be worn to prevent direct skin contact with the mist. Selecting gloves appropriate for the specific cutting fluid and the duration of exposure is vital.
- Eye Protection: Safety glasses or goggles, preferably with side shields, are essential to protect the eyes from mist splashes.
- Protective Clothing: Work uniforms made of materials that repel or resist the mist can reduce skin contact and provide an extra layer of protection.
Staying Safe, Staying Informed: The Importance of Continuous Monitoring and Education
Implementing and maintaining effective control measures is not a one-time endeavor. Continuous monitoring and periodic evaluations are critical to ensure the effectiveness of implemented solutions and identify potential problem areas. This includes air quality monitoring to measure mist concentration levels and ensuring that PPE remains adequate and in good condition.
Regular training for employees is also crucial. They should be educated about the hazards associated with lathe accident mist, the importance of following safety protocols, proper use of PPE, and how to recognize potential health issues. Open communication and a culture of safety within the workplace create a more proactive and effective safety environment.
Looking Ahead: The Future of Lathe Accident Mist Control
Research and innovation are constantly pushing the boundaries of lathe accident mist control. New, environmentally-friendly cutting fluids are being developed that create less mist and pose a lower health risk. Advanced engineering controls like robotic arms and automated systems are also reducing human exposure to mist. Ongoing research into nanotechnology and filtration methods promises even more effective and efficient solutions in the future.
Lathe Accident Mist
Conclusion: A Silent Danger, a Shared Responsibility
The invisible threat of lathe accident mist underscores the need for vigilant safety practices in workshops and manufacturing facilities. Recognizing the health risks, implementing preventative measures, and prioritizing worker education are crucial to ensure a safe and healthy working environment. By understanding the complexity of this issue and working together, we can minimize the impact of this silent danger and protect the well-being of those who power our industrial world.