Imagine a world where materials can withstand extreme temperatures, resist wear and tear, and even repel corrosion. This isn’t science fiction; it’s the reality of thermal spray technology. I first encountered its potential while researching a project on enhancing the durability of engine components. The sheer diversity of applications and the innovative techniques used in the field were truly fascinating. From aerospace and automotive to biomedical and energy industries, thermal spray technology has emerged as a vital tool for improving material performance and extending their lifespan.
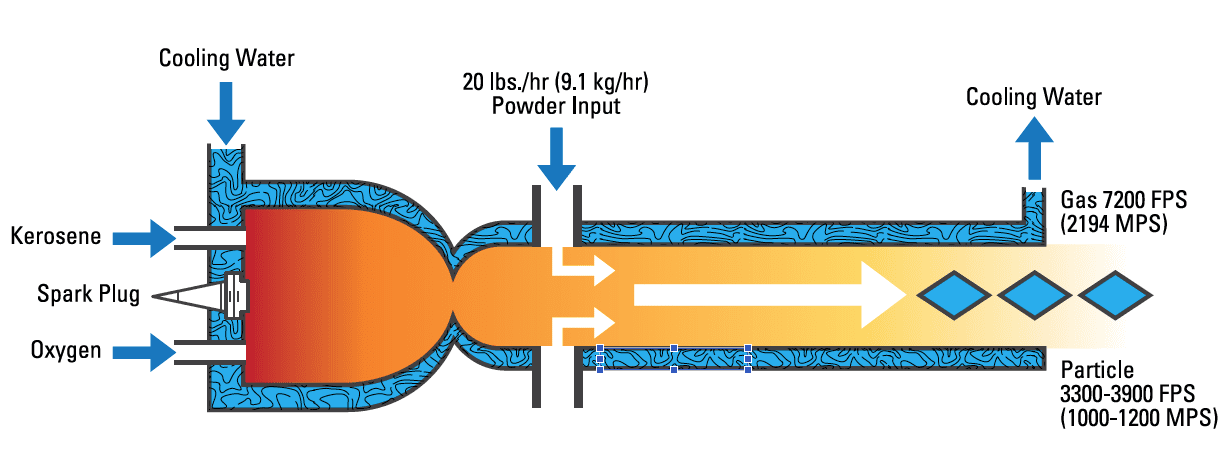
Image: extremecoatingsindia.com
The Journal of Thermal Spray Technology, as its name suggests, stands as a cornerstone of knowledge dissemination in this field. It acts as a platform for researchers, engineers, and practitioners to share their latest findings, discuss cutting-edge developments, and shape the future of thermal spray technology.
Exploring the World of Thermal Spray Technology
Definition and History
Thermal spray technology involves applying a coating to a substrate by propelling molten or semi-molten material onto its surface. This process creates a thin, durable layer that can significantly alter the substrate’s properties. The history of thermal spray technology dates back to the early 20th century, with its roots in the development of flame spraying. Over the years, various techniques have been developed, including wire arc spraying, plasma spraying, and high-velocity oxy-fuel (HVOF) spraying.
Applications and Benefits
Thermal spray coatings have a wide range of applications across diverse industries, offering numerous benefits:
- Enhanced Wear Resistance: Coatings can significantly reduce wear and tear, extending the lifespan of components and machinery.
- Improved Corrosion Resistance: Thermal spray coatings act as a barrier against corrosive environments, protecting metal surfaces from degradation.
- Enhanced Thermal Protection: These coatings can withstand high temperatures, protecting components from heat damage and increasing their operating life.
- Surface Modification: Thermal spraying allows for the modification of surface properties, including hardness, friction, and electrical conductivity.
- Repair and Restoration: Damaged or worn components can be restored to their original condition through thermal spray coating.
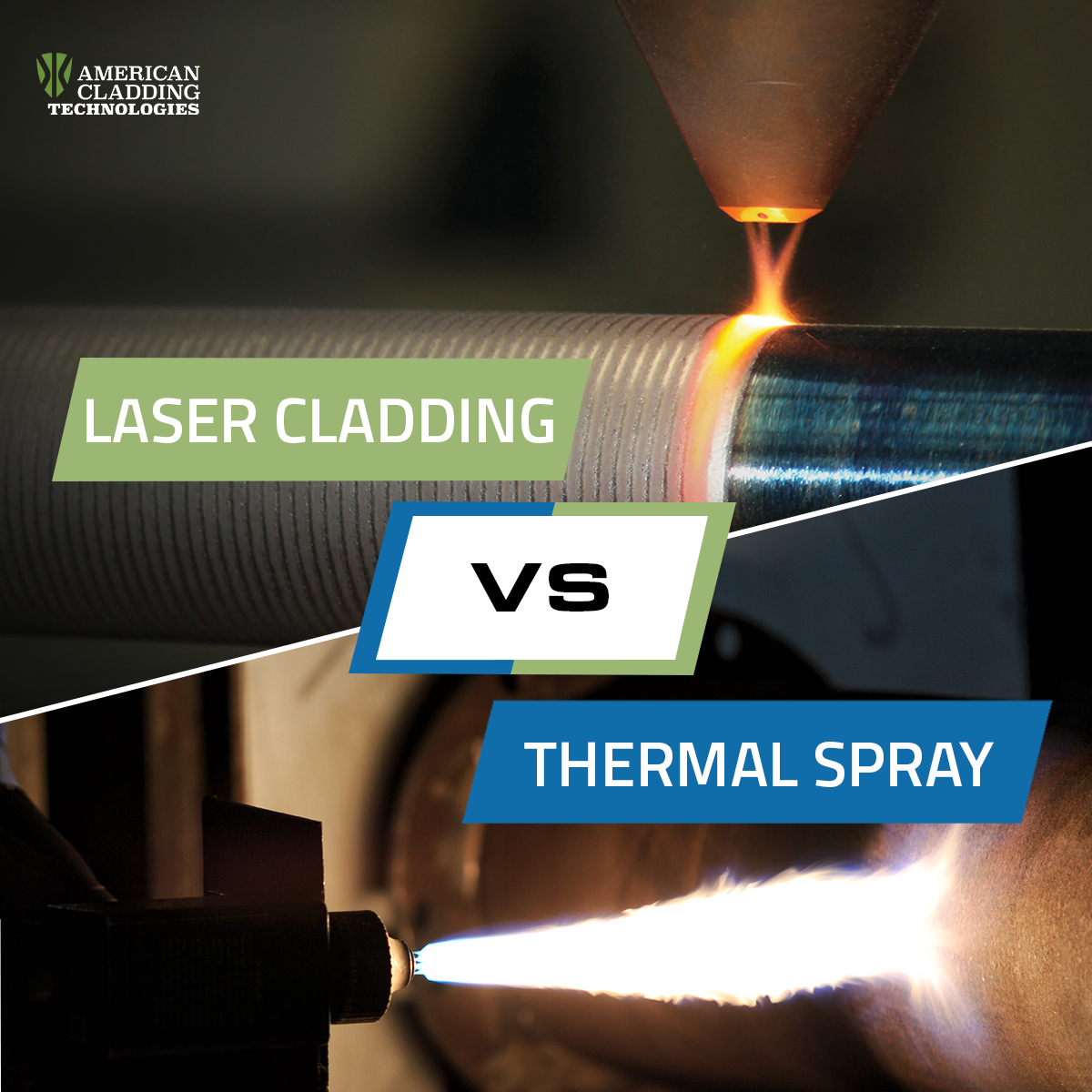
Image: americancladding.com
Types of Thermal Spray Processes
The choice of thermal spray process depends on the desired coating properties and the specific application. Here’s a breakdown of some commonly used techniques:
- Wire Arc Spraying: A process that uses an electric arc to melt wire feedstock, spraying it onto the substrate.
- Plasma Spraying: This method utilizes a high-temperature plasma to melt and propel powder feedstock onto the surface.
- High-Velocity Oxy-Fuel (HVOF): This technique utilizes a high-speed combustion flame to propel powdered feedstock onto the substrate, resulting in dense and highly-bonded coatings.
- Detonation Spraying: A process that utilizes supersonic combustion to propel powdered feedstock, creating highly-bonded coatings with excellent properties.
Current Trends and Innovations
Thermal spray technology continues to evolve at a rapid pace, driven by advancements in materials science, process control, and computational modeling. Some key trends shaping the field include:
- Nanostructured Coatings: The use of nanomaterials in thermal spray coatings is opening up new possibilities for enhancing wear and corrosion resistance, as well as functional properties like electrical conductivity and antibacterial activity.
- Additive Manufacturing Integration: Combining thermal spraying with additive manufacturing techniques provides new avenues for creating complex and customized coatings with tailored properties.
- Hybrid Coatings: A growing trend involves combining different thermal spray processes or applying multiple coatings in layers to achieve improved performance and functionality.
- Process Optimization and Simulation: Computational modeling and simulation play a crucial role in optimizing thermal spray processes, predicting behavior, and developing new applications.
Tips and Expert Advice for Researchers and Practitioners
As a researcher and blogger focusing on thermal spray technology, I’ve gained valuable insights from interacting with professionals in the field. Here are some tips I’ve found useful:
- Stay Updated with Latest Research: The Journal of Thermal Spray Technology and other reputable publications are your primary sources for staying informed about cutting-edge research and technological advancements.
- Engage in Industry Conferences: Attending conferences and workshops provides opportunities to network with experts, learn about new applications, and explore potential collaborations.
- Collaborate with Material Scientists: Consulting with materials scientists is crucial for selecting the optimal coating materials and understanding their behavior in different environments.
- Focus on Process Control: Achieving consistent and high-quality coatings requires meticulous process control and careful monitoring of parameters like temperature, pressure, and feedstock composition.
- Invest in Simulation and Modeling: Computational tools can significantly enhance your understanding of coating behavior, optimize process parameters, and develop new applications.
These tips, combined with a passion for continuous learning and innovation, can propel your career in the exciting field of thermal spray technology. It’s an area where you can make a real difference by developing advanced materials and applications that address critical engineering challenges.
Frequently Asked Questions (FAQ)
What are the key advantages of using thermal spray coatings?
Thermal spray coatings offer numerous advantages, including enhanced wear resistance, improved corrosion protection, increased thermal protection, surface modification, and repair/restoration capabilities, making them highly valuable across various industries.
How do I choose the right thermal spray process for my application?
The selection of a thermal spray process depends on the specific requirements of your application. Factors like desired coating properties, substrate material, and operating environment play a critical role. Consulting with experts and reviewing relevant literature can help you make an informed decision.
What are the challenges associated with thermal spray technology?
While thermal spray technology offers significant benefits, it also presents challenges like ensuring proper adhesion and porosity control, optimizing coating thickness and uniformity, and overcoming limitations in processing complex geometries.
Where can I find more information about thermal spray technology?
The Journal of Thermal Spray Technology, along with other reputable publications, industry associations, and online resources, provide comprehensive information and insights into thermal spray technology.
Journal Of Thermal Spray Technology
Conclusion
The Journal of Thermal Spray Technology serves as a vital resource for researchers and practitioners in this field, providing a platform for sharing knowledge and driving innovation. By staying updated with the latest advancements, engaging in collaborative efforts, and focusing on process control and optimization, you can contribute to the exciting advancements in the field. Are you interested in exploring this dynamic world of coatings and innovations further?