Picture this: you’re excitedly unwrapping a brand-new gadget you’ve been saving up for. It’s sleek, innovative, and promises to revolutionize your life. You spend hours setting it up, only to find it malfunctions within days. That’s the harsh reality of product failures, and it’s something that businesses and consumers alike want to avoid. But how do we prevent them? This is where the vital field of failure analysis and prevention comes in, and it’s a topic we’ll explore in detail.
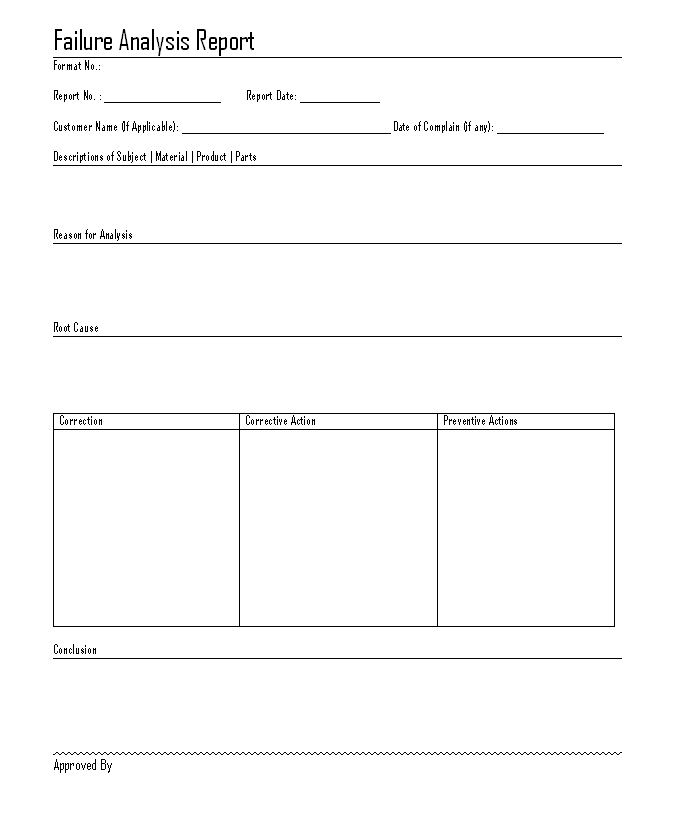
Image: limblecmms.com
The “Journal of Failure Analysis and Prevention” may sound like a dry, technical read, but it’s actually a fascinating window into the world of product reliability. Think of it as a detective agency for malfunctioning products. It delves into the root causes of failures, investigates materials and manufacturing processes, dissects failure modes, and ultimately helps devise strategies to prevent future incidents.
Understanding the Field of Failure Analysis and Prevention
What is Failure Analysis and Prevention?
Failure analysis and prevention (FAP) is a systematic and scientific discipline that examines the reasons behind product malfunctions or failures. It’s not just about identifying the problem, but also about understanding the why and how behind it. By analyzing failed components, materials, or systems, FAP experts can pinpoint the exact cause of failure, from design flaws to manufacturing defects to environmental factors.
The Importance of Failure Analysis and Prevention
FAP holds immense significance in various industries, from manufacturing and aerospace to automotive and electronics. It’s an essential tool for improving product reliability, minimizing risks, and ultimately enhancing customer satisfaction. Imagine the consequences of a faulty medical device or a malfunctioning aircraft. Failure analysis is crucial for identifying and addressing these issues before they become catastrophic.
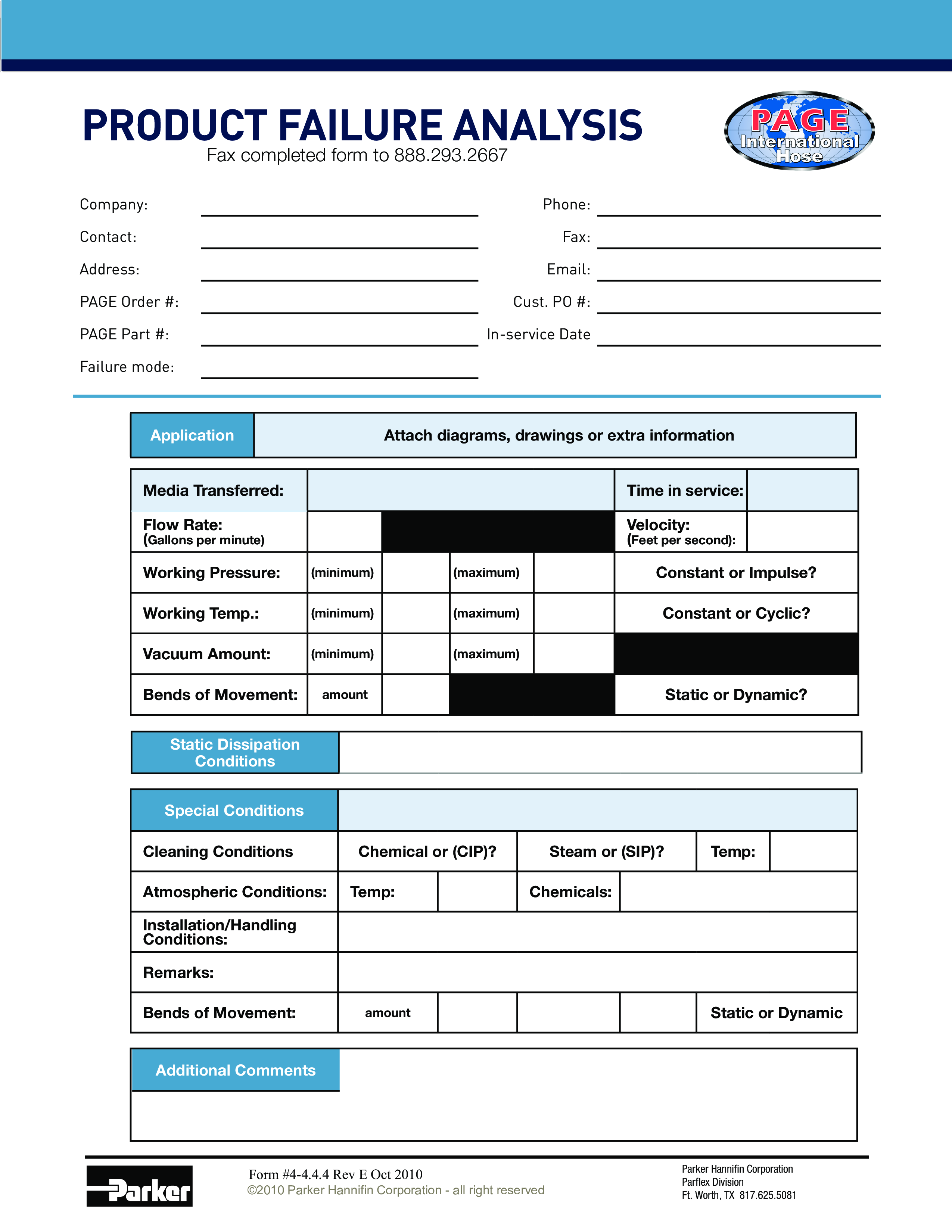
Image: ekdoseispelasgos.blogspot.com
The Process of Failure Analysis and Prevention
The FAP process typically involves the following stages:
- Problem Identification: Recognizing the failure and documenting its symptoms and conditions.
- Data Collection: Gathering information through visual inspection, destructive analysis, material testing, and environmental analysis.
- Analysis: Using scientific methods and engineering principles to interpret the collected data and identify the root cause of the failure.
- Solutions and Recommendations: Developing preventive measures, modifying designs, or improving manufacturing processes to eliminate the failure mechanism.
Key Techniques in Failure Analysis
Failure analysis employs a multitude of techniques depending on the nature of the failure and the materials involved. Some common methods include:
- Microscopy: Using microscopes to examine the microstructure of materials and identify defects or fracture patterns.
- Chemical Analysis: Identifying the chemical composition of materials using techniques like X-ray diffraction and spectroscopy.
- Mechanical Testing: Assessing the strength, hardness, and other mechanical properties of materials to understand failure mechanisms.
The Latest Trends in Failure Analysis and Prevention
FAP is a constantly evolving field, driven by advancements in technology and the increasing complexity of products. Here are some emerging trends:
- Predictive Maintenance: Utilizing data and analytics to predict potential failures and proactively schedule maintenance, reducing downtime and costs.
- Artificial Intelligence (AI): AI is being used to analyze vast amounts of data from sensors and simulations to identify potential failure risks and predict failure probabilities.
- Digital Twins: Creating virtual representations of physical products and using simulations to analyze and prevent potential failure modes.
Tips and Expert Advice for Implementing FAP
Implementing a robust FAP program requires a comprehensive strategy and a dedicated team. Here are some key tips:
- Establish a Culture of Prevention: Encourage employees at all levels to report potential problems and be proactive about identifying and addressing risks.
- Invest in Training and Expertise: Ensure your team has the necessary skills and knowledge to conduct proper failure analysis and implement preventive measures.
- Utilize Advanced Technologies: Embrace modern analytical techniques and tools to enhance your ability to diagnose failures and predict potential problems.
- Collaborate with Suppliers: Work closely with your suppliers to ensure they share your commitment to quality and reliability and have robust FAP programs of their own.
Why is it crucial to implement a robust FAP program?
A strong FAP program is not just a reactive measure; it’s a proactive approach that can prevent costly downtime, product recalls, and reputational damage. By analyzing failures and implementing corrective actions, businesses can ensure product reliability, enhance customer trust, and gain a competitive edge.
FAQ
Q: What are the common causes of product failures?
A: Product failures can arise due to various factors, including:
- Design flaws: Inadequate material selection, poor component design, or incorrect calculations.
- Manufacturing defects: Errors in assembly, welding, or material handling can introduce defects that cause premature failure.
- Environmental factors: Extreme temperatures, humidity, or vibration can degrade materials and lead to failure.
- Improper use or maintenance: Negligence or misuse of the product can accelerate wear and tear and cause premature failure.
Q: How can businesses benefit from Failure Analysis and Prevention?
A: Implementing FAP can bring numerous benefits, including:
- Improved product reliability: Reduced failures mean increased customer satisfaction and loyalty.
- Reduced warranty costs: Identifying and preventing failures early can significantly reduce warranty claims.
- Enhanced product safety: FAP plays a vital role in identifying and eliminating potential safety hazards.
- Competitive advantage: A strong commitment to quality and reliability can set a business apart in the market.
Journal Of Failure Analysis And Prevention
Conclusion
The Journal of Failure Analysis and Prevention is an essential resource for anyone involved in product development, manufacturing, and reliability. By understanding the principles of failure analysis and implementing robust preventive measures, businesses can minimize risks, enhance product performance, and ultimately achieve success. Are you interested in learning more about the fascinating world of failure analysis and prevention?